May 27, 2014 — Last month, a researcher at the National Renewable Energy Laboratory in Golden, Colo., loaded a postage stamp–sized solar cell onto a tray and placed it under a high-intensity pulse solar simulator. The simulator flashed a 2.5 millisecond pulse of light, and 19 mirrors reflected the photons down onto the cell. For a few more milliseconds, data funneled through a looping nest of wires into NREL computers. Researchers crunched and corrected the numbers, and device performance supervisor Keith Emery verified them: A new world record for solar photovoltaic efficiency had been set.
In the high stakes, highly technical world of photovoltaics, score is kept as the percent of the raw solar energy hitting a cell that is converted to electricity. Because his lab is the only one in the U.S. certified by the International Electrotechnical Commission for testing the efficiencies of solar cells, Emery is the nation’s unofficial solar scorekeeper.
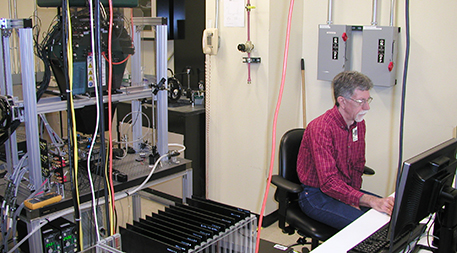
The National Renewable Energy Laboratory’s Tunable – High Intensity Pulsed Solar Simulator is in high demand these days as the testing ground for increasingly efficient solar photovoltaic innovations. Photo courtesy of NREL.
We’re in a Renaissance period of photovoltaic research, in which constant innovation is driving up efficiencies across all types of solar cells — from the most conventional crystalline silicon, to thin-film cadmium telluride, to much-buzzed-about new discoveries such as perovskite cells. World records are being broken at a breakneck rate, and the researchers behind this latest record-setter know better than to celebrate for too long.
The Goal: Grid Parity
Just about everyone in the photovoltaic community — even those left in the dust by the latest innovations — agrees that this constant one-upmanship is a very good thing. For the solar industry, efficiency ratings are far more than bragging rights or fodder for research grant proposals. They are key to moving closer to “grid parity” — the point at which the electricity photovoltaics produce costs the same as (or less than) that from coal and natural gas plants.
“When you can develop solar cells that have super high efficiency, you unlock savings across the board,” says physicist John Rogers of the University of Illinois at Urbana‑Champaign, a widely-revered leader in photovoltaic research. “You reduce the number of modules you build. You reduce the installation cost. Maintenance cost goes down. The amount of land you need goes down.”
The rule of thumb in the solar energy world is that photovoltaics will be able to compete directly with coal and natural gas when their cost of electricity production reaches $1 per watt.“The fundamental assumption is that when you bring something down to grid parity, the acceptance of the technology is much better,” says Ramamoorthy Ramesh, founding director of the U.S. Department of Energy’s SunShot program, which launched in 2011 with the mission of bringing the cost of solar power down to meet or beat the cost of electricity from fossil fuels.
The rule of thumb in the solar energy world is that photovoltaics will be able to compete directly with coal and natural gas when their cost of electricity production reaches $1 per watt. At the time SunShot started, the cost of solar PV electricity was $5 per watt. Three years on, Ramesh reports costs have already dropped to around $2.80 per watt. Most of the low-hanging fruit for cost savings has already been picked, however, and a glut of Chinese solar panels has been a big driver of solar affordability. To shave off the next $1.80, producing cells with higher efficiencies and moving those discoveries from the lab to the real world will be essential.
“With photovoltaics, we know what to do,” says Ramesh. “We need to reduce the costs of manufacturing and improve efficiency.”
Opportunities for Efficiency
Opportunities for improving efficiency are many. One important area of focus is on the semiconductor material used to capture light energy and turn it into current. Each material used as a semiconductor has unique strengths and limitations with regards to efficiency, typically because each is best at absorbing a certain segment of the natural light spectrum — so the search is constantly on for materials that can do a little better.
In order to maximize efficiency, engineers are constantly tinkering with every aspect of these microscopic cells.Other factors affect the end efficiency of a cell as well: how a semiconductor material degrades over time, how the architecture of the cell allows for absorption, how aptly electrodes capture the current the semiconductor creates and steer it to a productive use as electricity. In order to maximize efficiency, engineers are constantly tinkering with every aspect of these microscopic cells — altering chemistries and designs to ultimately produce the best current and voltage.
Because of the various potential efficiencies of different materials and designs, a record-setting efficiency score for a certain class of photovoltaic cell could be far higher than another. The best thin-film solar cells in the world max out around 23 percent, whereas the best silicon-based cells achieve around 26 percent and the best multi-junction cells (which use an assortment of semiconductors stacked atop one another) are clearing 44 percent.
But multi-junction cells are much more expensive to produce, and can’t really be used in widespread rooftop settings. So a silicon cell that logs better than 25 percent efficiency is every bit as exciting and promising as a multi-junction cell that’s clocking over 40.
Silicon Subs
When you picture a solar panel — on a rooftop or in a big sprawling photovoltaic farm — chances are you’ve got an image of crystalline silicon in your head. For decades, silicon has been the workhorse of photovoltaics worldwide, by far the most common semiconductor for solar cells. “Silicon has been around 80 to 90 percent of the market for something like 20 years,” says Sarah Kurtz, manager of the Reliability Group at NREL.
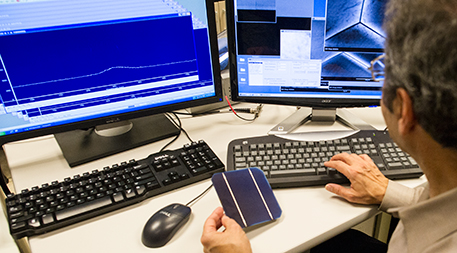
A TetraSun solar photovoltaic cell undergoes testing at the National Renewable Energy Laboratory in Golden, Colo. Photo by Dennis Schroeder / NREL.
Through those decades, the efficiencies of silicon cells have increased steadily, but slowly, and the prevailing attitude was that there wasn’t a whole lot more efficiency that could be coaxed out of silicon. Until recently.
An upstart silicon company, TetraSun, has NREL researchers abuzz and competitors seeing red. By turning a couple of silicon conventions on their ear, TetraSun logged 21 percent efficiency in just 18 months of work. While that might not sound like a lot, it’s already beating out typical screen-printed silicon cells — by far the most common you see on rooftops — by some serious percentage points.
Part of TetraSun’s secret is that of some notorious performance athletes: doping. All silicon wafers are doped (chemically treated), but TetraSun’s so-called “N-type” cells are doped with phosphorus. This prevents the cells from suffering the same light-induced degradation that plagues conventional boron-doped “P-type” wafers, helping keep efficiencies high longer into a panel’s lifespan.
Such efforts to substitute less expensive materials for pricey components are becoming increasingly important as companies look to building larger solar photovoltaic installations.
TetraSun’s N-type cells are also double-sided, featuring some clever architecture that allows the semiconductor to capture indirect sunlight that bounces off the bottom of the module. And, on top of that, TetraSun swapped out the silver grid that lines the front of a typical silicon photovoltaic panel, funneling the electric current off of the cell, for copper electrodes. It wasn’t really that simple — for months and months TetraSun’s engineers worked with NREL experts to figure out how to get the copper, a rather unruly material, to behave. Finally, the copper stuck in formation, the gridded lines about one-twenty-fifth the width of a human hair.
Such efforts to substitute less expensive materials for pricey components are becoming increasingly important as companies look to building larger solar photovoltaic installations, NREL analytical microscopy supervisor Mowafak Al-Jassim told SolarReviews last November.
As of February, panels equipped with TetraSun’s copper-lined cells are soaking up the rays on the rooftops of real paying customers. The company was bought by First Solar, a big-time player in commercial solar, which immediately rolled out TetraSun’s product as its first line for rooftops.
Rising Star
If silicon researchers are trying to teach an old dog new tricks, a new solar material called perovskite is a new exotic canine breed that is turning heads and dropping jaws. Perovskite cells (named after a mineral found in the Ural Mountains) are shooting up the efficiency charts faster than anything the photovoltaic world has ever seen.
It wasn’t until 2009 that perovskite was even considered as a semiconductor in solar cells. At that time, a Japanese scientist experimenting with it logged 3.8 percent efficiency. Last month, a team at the University of California–Los Angeles reported 19.3 percent.
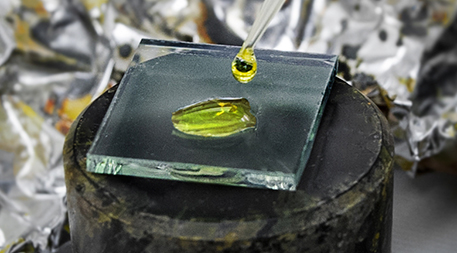
Relatively easy and inexpensive to produce, solar cells using perovskite as a semiconductor hold promise for moving photovoltaics toward grid parity. Photo by Dennis Schroeder / NREL.
Perovskite cells “are a variation on dye-sensitized cells, which have been worked on for quite some time,” explains Kurtz, referring to an emerging class of cells that essentially replaces the solid-state semiconductor wafers with light-absorbing organic dyes. “Just in the last year [researchers] figured out a material combination that allows a higher efficiency.” And ever since, it’s been off to the races.
The biggest advantage of perovskite is how easy it is to work with. It can be grown in a liquid and basically printed onto a base material, making for simple and cheap solar cell production that is easily transferred from high-tech research labs to factories.
One problem: the best-performing perovskite cells are blended with lead, which may work in the secure confines of a lab, but which nobody is going to put on their rooftops. In the past month, however, two separate research teams have published promising results of early experiments blending perovskite with tin. Tin is not only safer and more environmentally friendly than lead, it’s also much cheaper.
“Tin is a very viable material, and we have shown the material does work as an efficient solar cell,” said Mercouri Kanatzidis, a chemist at Northwestern University in a statement last month announcing his team’s findings. “Tin and lead are in the same group in the periodic table, so we expect similar results.”
Whether perovskite solar cells find success is, of course, an open question. The cells have yet to prove their viability in actual glass and metal modules, and the entire field is too young to have any sense of how well they hold up over time.
Stacking Cells
For Rogers, stacking cells is the way to break through the efficiency limits of traditional photovoltaics. Any given solar cell material (such as silicon or cadmium telluride, the most popular form of thin film), Rogers explains, is great at absorbing a certain limited portion of the sun’s light spectrum. Because they are only tuned into those wavelengths, however, all basic solar cells have a theoretical limit. (Crystalline silicon’s is around 29 percent, known in the field as the Shockley-Queisser limit.)
Rogers’ strategy is to stack different materials — each layer picking up a different chunk of the light spectrum.“The way you improve efficiency is to design solar cells that have the ability to operate across the full spectral range associated with incoming photons from the sun, and that’s a pretty broad range,” says Rogers.
Rogers’ strategy is to stack different materials — each layer picking up a different chunk of the light spectrum. “You can develop a solar cell that works really well in the green but lousy in the red,” he explains, “but then stack on another that is tuned to operate effectively in the red.”
The resulting semiconductor stacks are tiny — less than a millimeter square each — but the glass panel that rests over them contains lenses that focus the sun’s light directly onto each stack, like a bad kid torching a bug with a magnifying glass. Every bit of light that hits the panel meets a miniscule stack of cells.
This feat of microengineering — which, to brutally oversimplify it, involves growing each layer on a different substrate, etching away the desired cells, “rubber stamping” the semiconductors onto the cell itself and then stacking them four layers thick — actually works. Rogers’ team just announced a four-layer cell that clocked in in the lab at 42.5 percent efficiency.
Rogers is now working with a North Carolina–based company called Semprius to put multi-junction cells like his into field-ready modules. Even with all the assorted paraphernalia, Semprius modules are achieving 35 percent efficiency, which is “absolutely the highest performing module out there,” says Rogers. “It’s not even close.”
Homeowners probably won’t be placing an order with Semprius, because these modules aren’t for rooftops. They’re “most well suited for utility scale solar farms, or you can imagine them installed in industrial parks and data farms. We’re talking about ultra-low cost, large-scale power generation,” says Rogers.
Low enough cost to achieve grid parity? Siemens, the massive German solar leader, thinks so. The company is an early investor in Semprius, and Rogers calls its evaluation of the technology “most inspiring.”
“They took a look and said this could be cheaper than coal.”
And yet, true to the nature of the quest for better photovoltaics, this is not the end of the story: Back in the lab, Rogers says that with some minor tweaks his team will be able to get the efficiency rating up over 50 percent. “We can go a long way without another breakthrough.”
Ensia shares solutions-focused stories free of charge through our online magazine and partner media. That means audiences around the world have ready access to stories that can — and do — help them shape a better future. If you value our work, please show your support today.
Yes, I'll support Ensia!
Wow...a very nice article, but unfortunately you have been misguided by the technical people you talked to. Efficiency is actually not very important in the grand scheme of solar. I've published some articles on this. Over the last 40 years, the solar costs you mentioned ($/watt) has been cut in have seven time. That an unbelievable 128X reduction in cost. Do you know how much of that is due to efficiency? About 2X of the 128X. The rest come not from the PhDs mentioned in the article but from manufacturing cost reduction. Good old fashion low-cost, high-volume manufacturing. But manufacturing is not sexy and does not help get funding from the government that those research labs depend on. Sad but true. The U.S. might fail in solar production, not because of efficiency, but because of wrong thinking that you might have inadvertently added to. We need funding for taking these technologies already developed in the U.S. to manufacturing scale. It's manufacturing prowess and funding, not more science that is needed.
.59/Watt as of the time I'm posting this.